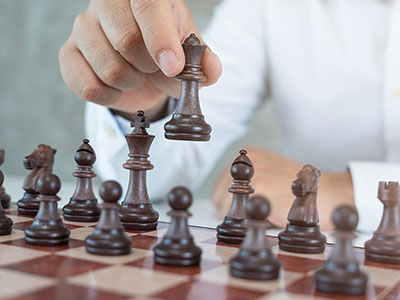
Supply chain risks are exploding. Just look at the news, and you’ll see a potential UPS strike, a Canadian port strike, potential hurricanes (Hawaii, Florida), China stirring up potential conflict with China, the Crimean bridge attack, and much more. Any one of these issues could have a detrimental impact on the economy and could put a business in the wake of the issue out of business. Clients must prioritize preparation and prevention of significant risks.
For example, when I was VP of Product Supply for a mid-market manufacturer, our largest production facility (70% of the volume) was located in an area that could flood due to hurricanes. The Board of Directors wasn’t happy about purchasing excess stock year after year in preparation for hurricane season although we made a good case for it and continued to prepare. It used cash that couldn’t be invested elsewhere.
One year, a hurricane arrived that completely flooded the area. The cars were under water at the airport and no one could get to work, let alone trucks arrive with materials or leave with shipments to customers. The products were used in hospitals and nursing homes and so lengthy delays were not acceptable. Luckily, the builders of the plant had the foresight to build on a hill so that it was one of the only buildings in the area not affected; however, employees could not get to and from work.
The backup plant went into overdrive with production although it couldn’t produce everything that the main facility could produce. Because prevention and preparation were a priority, as soon as the roads were passable, trucks could pick up the excess stock and production could start full force because raw materials were already on hand. Thus, we were able to supply our customers with seamless customer service.
Unfortunately, most clients and colleagues are not in this position. They must prioritize preparation and prevention.
Preparation & Prevention Priorities
Preparing in advance will be far less expensive than waiting to respond once the issue occurred with contingent action. Once the hurricane arrived, no suppliers could get through with raw materials. Even if they could, they would have multiple priorities for businesses impacted by the hurricane. Most likely, we would have ended up on a waiting list. The best case scenario is that we would have to pay expedite fees if we could gain priority, and we would have waited a week to several months to get the required materials. Worse than that, our customer service would have suffered and we might have lost customers.
In today’s supply chain, the risks are much higher and voluminous, Thus, instead of suffering these unacceptable consequences, executives must prepare.
- Safety stock: Safety stock of key items or at certain times of the year (such as hurricane season) or for key customers make sense.
- Treat key suppliers as partners: Suppliers are not going to come through for you if you treat them as a vendor. Instead treat them as partners so that they will come through for you when these risks occur. You most likely should cut back on the number of key / critical suppliers and increase your focus on these partnerships. Be upfront with them, hold them accountable but also share in wins and losses while working towards win-win solutions/ path forward.
- Safety preparedness: Think about how to build safety into your process; it is not a one-time activity, and it isn’t something you should prioritize after the fact.
- Risk assessments: Develop meaningful risk assessments. Unfortunately, I’ve seen many risk assessments throughout the years that were more of a “check the box” exercise and not a focus on which risks to prioritize with accountabilities for leaders to mitigate those risks. Lots of paperwork with little sustenance will not lead to success in the coming decade.
- Inspections: You should follow up the assessments with the appropriate inspections to ensure everything is in order. These can be physical inspections, process inspections and systems inspections. Every client will be in deep trouble if their ERP system or IT infrastructure goes down. Inspect your critical manual work processes, your backup systems, etc.
- Insurance: Get the appropriate types of insurance to protect your company. You will need property insurance, D&O, automobile (potentially), cyber, etc. It isn’t easy to get insurance when you need it. You must get insurance before you need it.
- Other forms of insurance: Consultants can have an insurance like quality. There has been significant turnover and transition occurring since the pandemic, and several clients have kept us on board as an “insurance” to run decisions by to gain additional insights and to jump in and fill gaps while upgrading processes as needed. Trusted advisors and consultants can fill these types of roles.
- Sprinkler systems: You should install “contingent actions” as well such as sprinkler systems although prevention is better than preparation in this case! When you need it, you must have these contingent actions “ready to go”.
Please contact us with your thoughts on preparation and prevention stories, issues, and ideas. And, please keep us in the loop of your situation and how we can help your organization prepare to thrive and mitigate your highest risks. We are introducing a new SIOP (Sales Inventory Operations Planning) assessment to ensure your supply chain is ready to support your growth plans while mitigating critical risks. Contact us if interested to discuss further. Learn more about these topics in our blog and download your complimentary copy of our recently released special report: The Road Ahead: Business, Supply Chain & The World Order.